Unlocking the Power of Welding WPS: Strategies for Efficiency and Safety in Fabrication
In the realm of fabrication, Welding Procedure Specifications (WPS) stand as the backbone of welding procedures, dictating the essential actions for attaining both performance and safety and security in the manufacture procedure. Comprehending the ins and outs of WPS is extremely important to utilizing its full possibility, yet many companies battle to open real power that lies within these files (welding WPS). By delving right into the strategies that maximize welding WPS, a world of boosted productivity and increased security waits for those going to explore the subtleties of this important element of fabrication

Relevance of Welding WPS
The relevance of Welding Treatment Specifications (WPS) in the fabrication market can not be overemphasized. WPS act as an important roadmap that describes the needed steps to ensure welds are performed continually and appropriately. By specifying essential specifications such as welding procedures, materials, joint designs, preheat temperature levels, interpass temperature levels, filler metals, and post-weld heat therapy requirements, WPS provide a standardized technique to welding that boosts performance, high quality, and safety in construction processes.
Adherence to WPS aids in accomplishing uniformity in weld high quality, minimizing the possibility of defects or architectural failures. This standardization likewise facilitates conformity with industry guidelines and codes, making certain that made frameworks fulfill the called for safety and security criteria. In addition, WPS documentation makes it possible for welders to reproduce effective welding treatments, leading to consistent results throughout various projects.
In significance, the meticulous advancement and rigorous adherence to Welding Procedure Specs are extremely important for upholding the stability of bonded structures, protecting against potential hazards, and maintaining the online reputation of fabrication business for supplying high-quality products and solutions.
Secret Aspects of Welding WPS

Enhancing Performance With WPS
When maximizing welding operations, leveraging the vital aspects laid out in Welding Treatment Requirements (WPS) becomes crucial for taking full advantage of and streamlining processes productivity. One method to enhance performance with WPS is by meticulously selecting the ideal welding criteria. By sticking to the certain guidelines given in the WPS, welders can make sure that the welding devices is set up appropriately, leading to constant and top quality welds. Furthermore, following the pre-approved welding series described in the WPS can dramatically lower the moment invested in each weld, eventually enhancing overall efficiency.
In addition, appropriate training and useful source certification of welders in understanding and executing WPS can additionally boost performance. Guaranteeing that all group participants are well-versed in analyzing and performing the WPS accurately can revamp and decrease mistakes, saving both time and resources. Consistently examining and updating the WPS to include any lessons found out or technological innovations can also add to efficiency renovations in welding procedures. By accepting the standards set forth in the WPS and continually seeking methods to maximize processes, makers can achieve greater performance levels and exceptional outcome.
Ensuring Safety And Security in Fabrication

Safety methods in construction play a critical role in guarding personnel and maximizing functional procedures. Guaranteeing safety in manufacture entails a diverse approach that incorporates numerous facets of the welding procedure. One fundamental aspect is the arrangement of individual protective devices (PPE) customized to the certain threats existing in the manufacture setting. Welders need to be outfitted with ideal equipment such as safety helmets, gloves, and safety clothing to minimize dangers connected with welding activities.
Additionally, adherence to correct air flow and fume extraction systems is crucial in preserving a healthy job atmosphere. Welding fumes contain harmful substances that, if breathed in, can pose severe health dangers. Implementing reliable air flow measures aids to reduce direct exposure to these harmful fumes, promoting respiratory system health amongst workers.
Normal devices upkeep and examinations are also necessary for ensuring safety in manufacture. Defective equipment can result in injuries and accidents, underscoring the significance of routine checks and prompt fixings. By focusing on precaution and promoting a society of awareness, construction centers can develop a safe and secure and productive workplace for their employees.
Implementing WPS Finest Practices
To boost functional efficiency and make sure top quality end results in manufacture procedures, incorporating Welding Procedure Specification (WPS) best practices is critical - welding WPS. Executing WPS finest techniques involves precise preparation, adherence to sector standards, and continuous monitoring to guarantee optimal outcomes. To start with, choosing the proper welding procedure, filler product, and preheat temperature specified in the WPS is vital for attaining the wanted weld top quality. Second of all, making sure that qualified welders with the required certifications accomplish the welding procedures according to the WPS standards is crucial for uniformity and dependability. Routinely updating and examining WPS files to reflect any procedure enhancements or modifications in materials is additionally a crucial finest practice to preserve accuracy and relevance. Additionally, giving thorough training to welding employees on WPS requirements and ideal methods fosters a society of security and quality within the manufacture atmosphere. By diligently carrying out WPS finest practices, makers can enhance their procedures, minimize mistakes, and provide remarkable products to fulfill customer expectations.
Conclusion
In verdict, welding WPS plays an essential function in making sure efficiency and safety and security in manufacture processes. By following these methods, organizations can unlock the complete possibility of welding WPS in their construction procedures.
In the world of manufacture, look at here Welding Treatment Requirements informative post (WPS) stand as the foundation of welding procedures, determining the needed actions for accomplishing both efficiency and safety in the fabrication process. By defining crucial parameters such as welding processes, materials, joint designs, preheat temperatures, interpass temperature levels, filler metals, and post-weld heat therapy needs, WPS give a standardized technique to welding that enhances performance, quality, and safety and security in construction procedures.
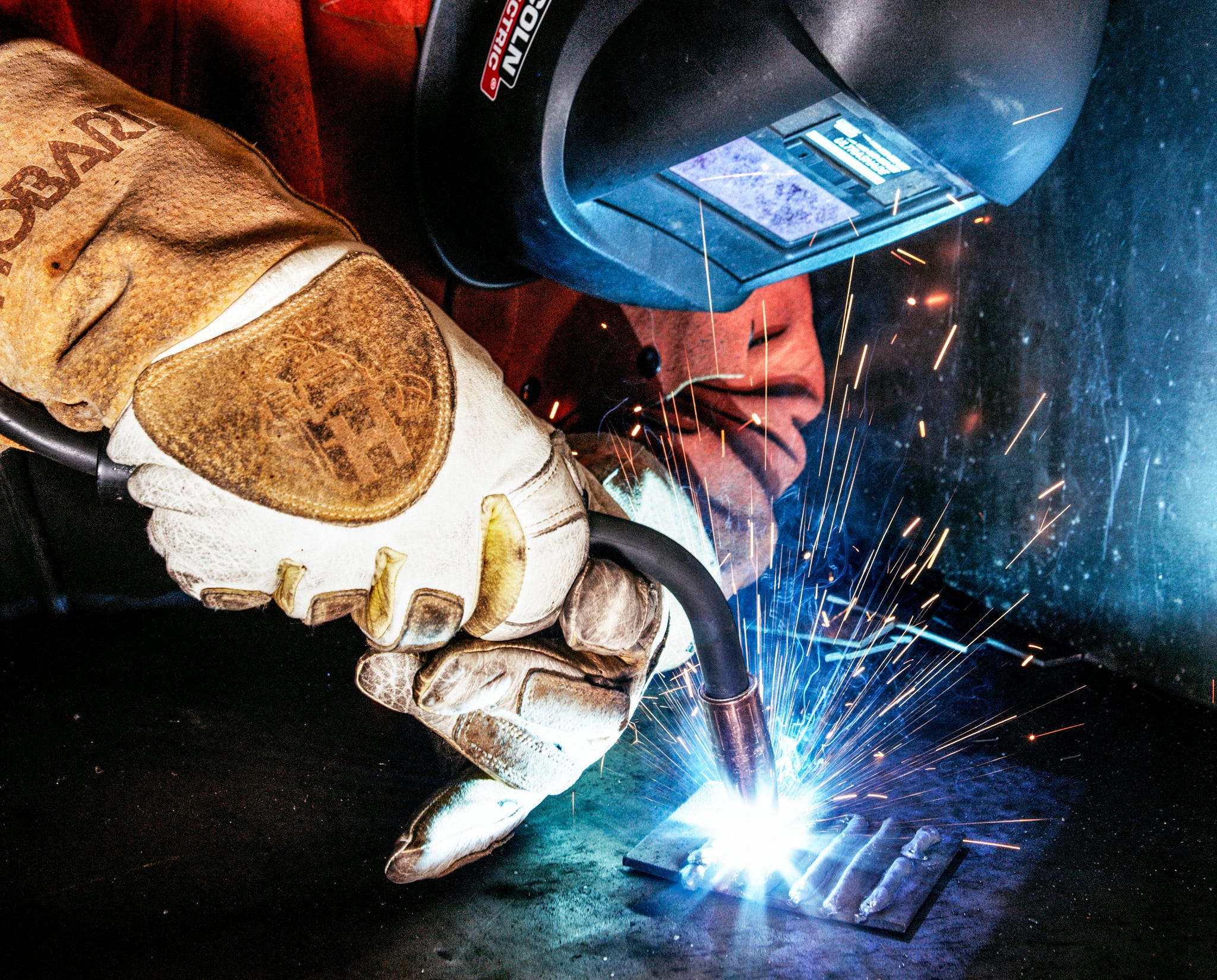
When maximizing welding operations, leveraging the crucial components outlined in Welding Procedure Requirements (WPS) becomes vital for taking full advantage of and simplifying processes productivity. (welding WPS)